Characteristics of plate-shaped alumina (plate-shaped corundum) and its application in refractory ma
2024-03-21 15:04:19
The application of plate-shaped alumina as refractory aggregate for large comprehensives began in the mid-1950s, when new refractory binders were developed, such as high-purity calcium aluminate cement and phosphate binders. The application of these binders greatly improves the corrosion resistance and wear resistance of plate-shaped alumina refractory materials.
<h3>1. Characteristics of plate alumina</h3>
Ordinary sintered alumina is generally fired in a rotary kiln or tunnel. Due to temperature restrictions, a small amount of sintering accelerators such as MgO, CaO, etc. are usually added to promote its density. Therefore, ordinary sintered alumina has low porosity and fine and dense crystals, resulting in poor thermal shock resistance.
Plate-shaped alumina is recrystallized α-Al2O3 that is rapidly fired and completely sintered at a high temperature above 1900°C. It does not contain any additives. Its microstructure has the following characteristics:
①Composed of well-developed α-Al2O3 crystals;
②α-Al2O3 crystals are coarse, with a median diameter of 40 to 200 μm. The two-dimensional morphology of the crystals is flat and intertwined;
③α-Al2O3 crystal contains many 5~15μm circular closed pores; while there are fewer open pores, generally 2%~3%;
④Due to the presence of α-Al2O3 (about 0.16%), β-Al2O3 exists in the structure, but it all grows at the grain boundaries of α-Al2O3 crystals.
Due to the above structural characteristics of wrench-shaped alumina, it has the following physical properties:
①High melting point, about 2040℃;
②High grain hardness, Mohs hardness 9, Knoop hardness 2000;
③ Resistant to chemical attack, except for hydrofluoric acid and phosphoric acid, most alkalis and mineral acids have no effect on plate-shaped alumina;
④ Since it does not have microcracks and large internal pores, its strength is high; at the same time, its strength does not drop much when subjected to thermal shock, so its thermal shock stability is good (see Table 1);
⑤High thermal conductivity and high resistivity, with good electrical properties at high frequency and high temperature.
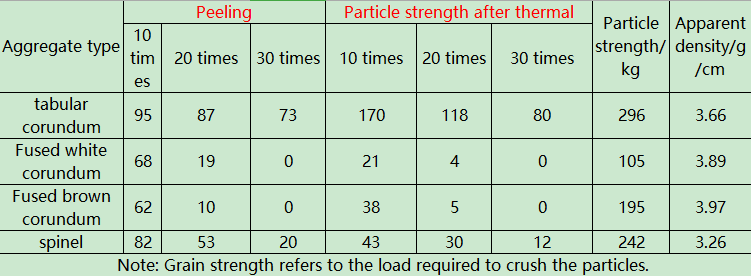
The typical properties of plate-shaped alumina are listed in Table 1. Plate-shaped alumina is mostly used as refractory aggregates, and is also used as an additive into the matrix. When combined with other refractory raw materials, it will have the following advantages: high refractoriness; thermal load strength High; small creep; high density; low air permeability; good thermal shock stability and wear resistance; low thermal shrinkage; high purity, reducing the impact of impurities on the high temperature performance of the material.
<h3>2. Application of plate-shaped alumina in refractory materials for the steel industry</h3>
Due to a series of strong properties of plate-shaped alumina, it becomes an ideal refractory raw material. It can be used as aggregate in refractory materials such as Al2O3-C, Al2O3-SiO2-C and Al2O3-Cr2O3, and can also be added to Among other high-aluminum unshaped refractory materials. Phosphate-bonded and calcium aluminate cement-bonded tabular alumina unshaped refractories are widely used. All areas where fused corundum or white corundum are used can be replaced with plate-shaped alumina to improve the performance of refractory materials.
The applications of plate alumina in the steel industry include almost everything from blast furnaces, hot blast furnaces, mixing furnaces, fish pots to converters, secondary refining furnaces, mold casting and continuous casting ladles, tundishes and soaking furnaces and heating furnaces and other parts that use alumina refractory materials.
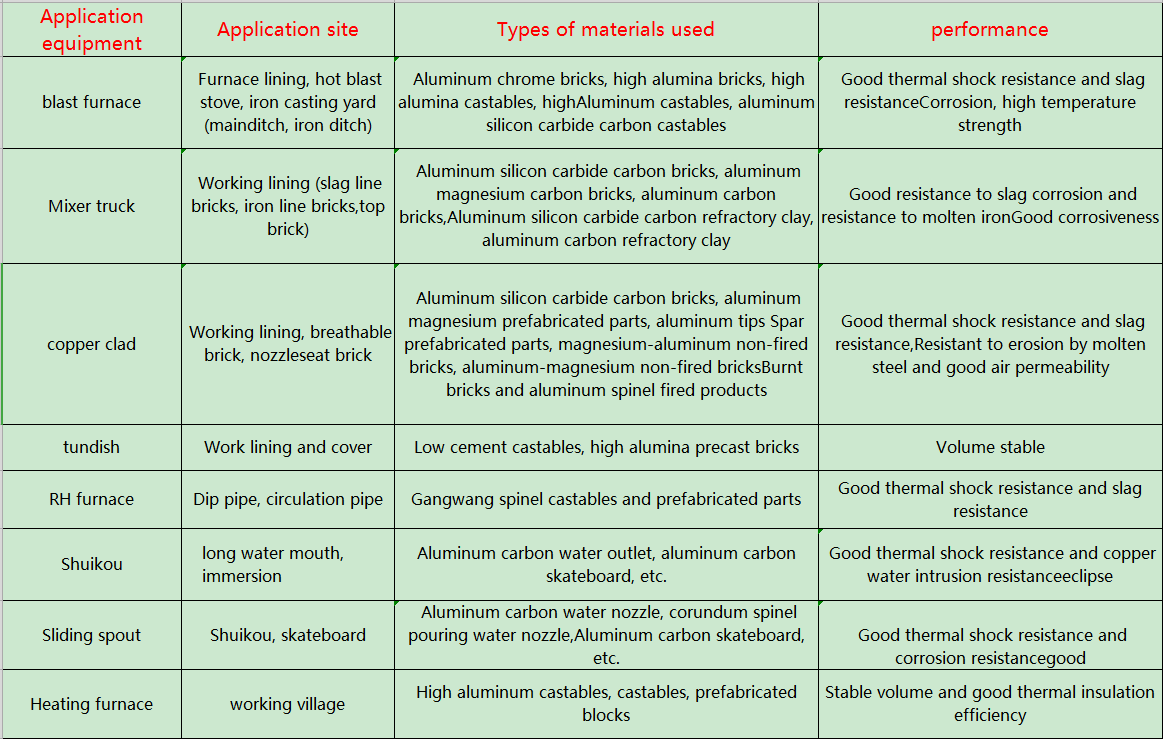
In the ceramic industry, plate alumina is used in kiln furniture to significantly improve its performance. For example, when used in ceramic rollers, its thermal shock stability and deformation resistance can be improved; when used in the manufacture of saggers and shed plates for high-temperature ceramics such as fired spark plugs and alumina balls, the service life is significantly improved. Plate alumina can also be used as insulators and catalyst carriers for high-temperature reactions that require low pores, high strength and high purity.
<h3>1. Characteristics of plate alumina</h3>
Ordinary sintered alumina is generally fired in a rotary kiln or tunnel. Due to temperature restrictions, a small amount of sintering accelerators such as MgO, CaO, etc. are usually added to promote its density. Therefore, ordinary sintered alumina has low porosity and fine and dense crystals, resulting in poor thermal shock resistance.
Plate-shaped alumina is recrystallized α-Al2O3 that is rapidly fired and completely sintered at a high temperature above 1900°C. It does not contain any additives. Its microstructure has the following characteristics:
①Composed of well-developed α-Al2O3 crystals;
②α-Al2O3 crystals are coarse, with a median diameter of 40 to 200 μm. The two-dimensional morphology of the crystals is flat and intertwined;
③α-Al2O3 crystal contains many 5~15μm circular closed pores; while there are fewer open pores, generally 2%~3%;
④Due to the presence of α-Al2O3 (about 0.16%), β-Al2O3 exists in the structure, but it all grows at the grain boundaries of α-Al2O3 crystals.
Due to the above structural characteristics of wrench-shaped alumina, it has the following physical properties:
①High melting point, about 2040℃;
②High grain hardness, Mohs hardness 9, Knoop hardness 2000;
③ Resistant to chemical attack, except for hydrofluoric acid and phosphoric acid, most alkalis and mineral acids have no effect on plate-shaped alumina;
④ Since it does not have microcracks and large internal pores, its strength is high; at the same time, its strength does not drop much when subjected to thermal shock, so its thermal shock stability is good (see Table 1);
⑤High thermal conductivity and high resistivity, with good electrical properties at high frequency and high temperature.
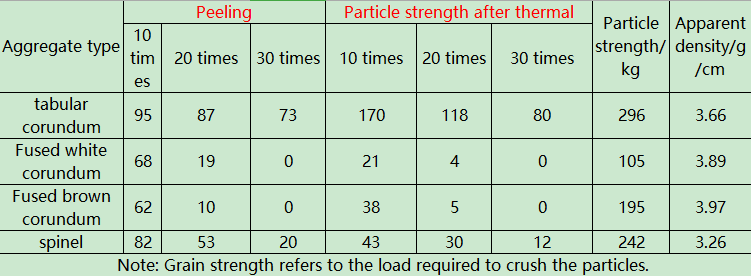
The typical properties of plate-shaped alumina are listed in Table 1. Plate-shaped alumina is mostly used as refractory aggregates, and is also used as an additive into the matrix. When combined with other refractory raw materials, it will have the following advantages: high refractoriness; thermal load strength High; small creep; high density; low air permeability; good thermal shock stability and wear resistance; low thermal shrinkage; high purity, reducing the impact of impurities on the high temperature performance of the material.
<h3>2. Application of plate-shaped alumina in refractory materials for the steel industry</h3>
Due to a series of strong properties of plate-shaped alumina, it becomes an ideal refractory raw material. It can be used as aggregate in refractory materials such as Al2O3-C, Al2O3-SiO2-C and Al2O3-Cr2O3, and can also be added to Among other high-aluminum unshaped refractory materials. Phosphate-bonded and calcium aluminate cement-bonded tabular alumina unshaped refractories are widely used. All areas where fused corundum or white corundum are used can be replaced with plate-shaped alumina to improve the performance of refractory materials.
The applications of plate alumina in the steel industry include almost everything from blast furnaces, hot blast furnaces, mixing furnaces, fish pots to converters, secondary refining furnaces, mold casting and continuous casting ladles, tundishes and soaking furnaces and heating furnaces and other parts that use alumina refractory materials.
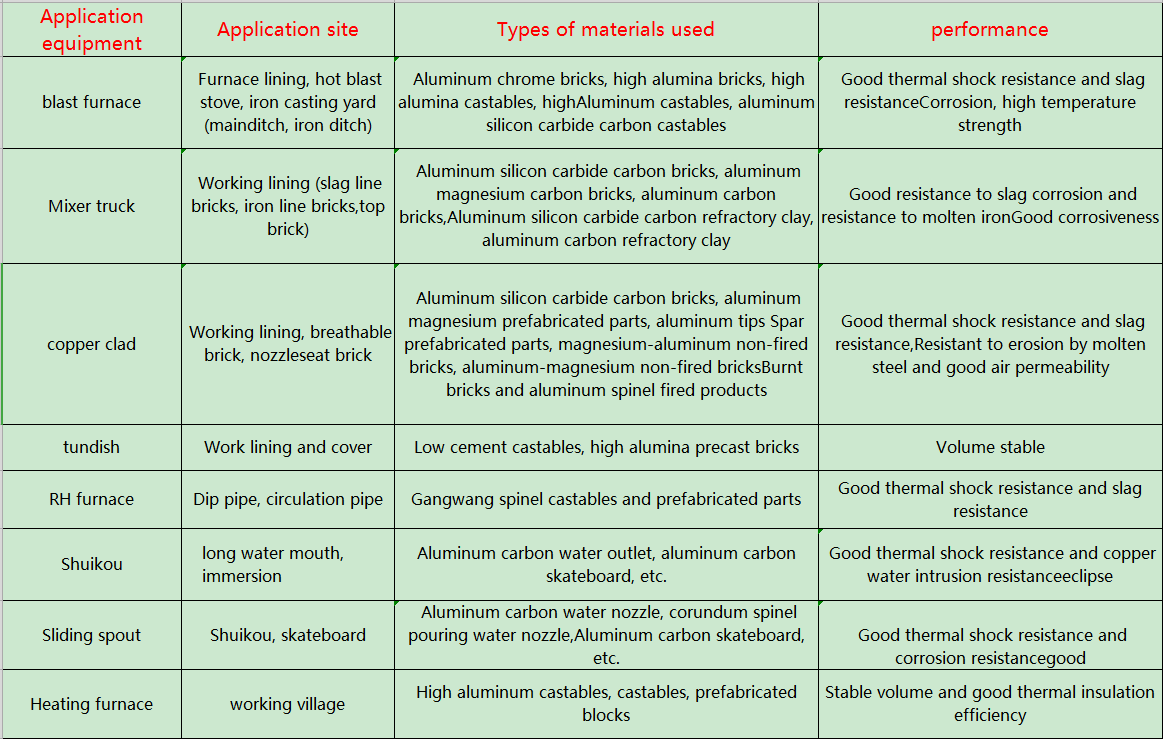
In the ceramic industry, plate alumina is used in kiln furniture to significantly improve its performance. For example, when used in ceramic rollers, its thermal shock stability and deformation resistance can be improved; when used in the manufacture of saggers and shed plates for high-temperature ceramics such as fired spark plugs and alumina balls, the service life is significantly improved. Plate alumina can also be used as insulators and catalyst carriers for high-temperature reactions that require low pores, high strength and high purity.